Counts Custom Cast: Your Ultimate Guide To Personalized Casting Solutions
Table of Contents
Introduction
Counts Custom Cast is a revolutionary approach to personalized casting solutions that cater to a wide range of industries and applications. Whether you're in manufacturing, art, or engineering, custom casting provides unmatched flexibility and precision. This guide dives deep into the world of Counts Custom Cast, exploring its benefits, applications, and how it can transform your projects.
Custom casting has been around for centuries, but modern technology has taken it to new heights. From intricate sculptures to industrial components, Counts Custom Cast offers tailored solutions that meet specific requirements. This process allows businesses and individuals to create unique products with exceptional detail and durability.
In this article, we will walk you through everything you need to know about Counts Custom Cast. From understanding the basics to exploring its future trends, we aim to provide valuable insights that align with the principles of E-E-A-T (Expertise, Authoritativeness, Trustworthiness) and YMYL (Your Money or Your Life). Let’s get started!
Read also:1965 Chinese Zodiac Unveiling The Year Of The Snake
What is Counts Custom Cast?
Counts Custom Cast refers to a specialized casting process where products are created based on custom designs and specifications. Unlike mass-produced items, custom casting ensures that every piece is unique and tailored to the client's needs. This process involves creating molds, pouring molten material, and allowing it to cool and solidify into the desired shape.
The term "Counts" in Counts Custom Cast highlights the precision and accuracy involved in the process. Every detail is carefully accounted for, ensuring that the final product meets the highest standards of quality. This method is widely used in industries such as automotive, aerospace, and art.
Key Features of Counts Custom Cast
- Customization: Tailored designs to meet specific requirements.
- Precision: High level of accuracy in every detail.
- Versatility: Suitable for a wide range of materials and applications.
- Durability: Strong and long-lasting final products.
Benefits of Custom Casting
Custom casting offers numerous advantages over traditional manufacturing methods. Here are some of the key benefits:
1. Unmatched Customization
With Counts Custom Cast, you can create products that are uniquely designed to fit your needs. Whether it's a specific size, shape, or design, custom casting allows for complete personalization.
2. Enhanced Precision
The process ensures that every detail is accounted for, resulting in products with exceptional accuracy. This is particularly important in industries like aerospace and medical devices, where precision is critical.
3. Cost-Effectiveness for Unique Projects
While custom casting may have higher upfront costs compared to mass production, it is more cost-effective for unique or low-volume projects. It eliminates the need for expensive tooling and reduces waste.
Read also:Doraemon The Beloved Anime Character That Captivates Generations
4. Wide Range of Materials
Counts Custom Cast supports a variety of materials, including metals, plastics, and composites. This versatility makes it suitable for diverse applications.
Applications of Counts Custom Cast
Counts Custom Cast is used in a wide range of industries and applications. Here are some of the most common ones:
1. Automotive Industry
Custom casting is widely used in the automotive sector to create engine components, chassis parts, and decorative elements. The precision and durability of custom-cast parts make them ideal for this industry.
2. Aerospace and Defense
In aerospace and defense, custom casting is used to produce lightweight yet strong components. These parts must meet strict quality and safety standards, making custom casting an excellent choice.
3. Art and Sculpture
Artists and sculptors often rely on custom casting to bring their creations to life. The process allows for intricate details and unique designs that are difficult to achieve with other methods.
4. Medical Devices
Custom casting is also used in the medical field to create prosthetics, implants, and surgical instruments. The ability to produce precise and biocompatible components is crucial in this industry.
How Does Custom Casting Work?
The custom casting process involves several steps, each critical to achieving the desired outcome. Here’s an overview of how it works:
1. Design and Prototyping
The process begins with creating a detailed design. This can be done using CAD software or traditional methods. A prototype is often created to test the design before moving forward.
2. Mold Creation
Once the design is finalized, a mold is created. This can be made from materials like sand, metal, or silicone, depending on the application.
3. Material Selection
The next step is selecting the appropriate material for the project. Factors such as strength, weight, and cost are considered during this stage.
4. Casting Process
The molten material is poured into the mold and allowed to cool and solidify. This step requires precision to ensure the final product meets the desired specifications.
5. Finishing Touches
After the casting is complete, the product undergoes finishing processes such as polishing, painting, or machining to achieve the desired appearance and functionality.
Choosing the Right Material
Selecting the right material is crucial for the success of a custom casting project. Here are some factors to consider:
1. Strength and Durability
For applications that require high strength and durability, materials like steel, aluminum, or titanium are often used.
2. Weight
In industries like aerospace, lightweight materials such as magnesium or composites are preferred.
3. Cost
Budget constraints may influence material selection. For example, plastic or resin may be more cost-effective for certain projects.
4. Corrosion Resistance
For outdoor or marine applications, corrosion-resistant materials like stainless steel or bronze are ideal.
Common Challenges and Solutions
While Counts Custom Cast offers numerous benefits, it also comes with challenges. Here are some common issues and how to address them:
1. Porosity
Porosity can weaken the final product. To prevent this, ensure proper mold design and control the casting process carefully.
2. Shrinkage
Shrinkage occurs when the material contracts during cooling. Using the right material and mold design can minimize this issue.
3. Surface Defects
Surface defects can be caused by poor mold quality or improper casting techniques. Regular maintenance and quality control can help prevent these issues.
Top Industries Using Custom Casting
Counts Custom Cast is widely used across various industries. Here are some of the top sectors benefiting from this technology:
1. Automotive
Custom casting is used to produce engine blocks, wheels, and other critical components.
2. Aerospace
Aerospace relies on custom casting for turbine blades, structural components, and more.
3. Art and Sculpture
Artists use custom casting to create intricate sculptures and installations.
4. Medical Devices
Custom casting is essential for creating prosthetics, implants, and surgical tools.
Cost Considerations
While custom casting offers numerous advantages, it’s important to consider the costs involved. Here are some factors that influence the cost:
1. Complexity of Design
More complex designs require more time and resources, increasing the cost.
2. Material Selection
High-quality or rare materials can significantly impact the overall cost.
3. Production Volume
Custom casting is often more cost-effective for low-volume projects compared to mass production.
4. Finishing Processes
Additional finishing steps like polishing or coating can add to the cost.
Future Trends in Custom Casting
The custom casting industry is constantly evolving, driven by advancements in technology and changing market demands. Here are some trends to watch:
1. 3D Printing Integration
3D printing is being integrated into the custom casting process, allowing for even more intricate designs and faster production times.
2. Sustainable Materials
There is a growing focus on using eco-friendly and sustainable materials in custom casting.
3. Automation and AI
Automation and artificial intelligence are being used to streamline the casting process and improve efficiency.
4. Customization for Consumers
With the rise of e-commerce, more consumers are seeking personalized products, driving demand for custom casting services.
Conclusion
Counts Custom Cast is a versatile and innovative solution that caters to a wide range of industries and applications. From automotive components to artistic sculptures, custom casting offers unmatched precision, customization, and durability. By understanding the process, benefits, and challenges, you can make informed decisions about incorporating custom casting into your projects.
We hope this guide has provided valuable insights into the world of Counts Custom Cast. If you have any questions or would like to share your experiences, feel free to leave a comment below. Don’t forget to share this article with others who might find it useful, and explore our other resources for more information on custom casting and related topics.
Bruce Dern: A Legendary Actor's Journey Through Hollywood
Parker Snovel: The Ultimate Guide To The Rising Star
Who Is Eric Prince? A Comprehensive Guide To His Life, Career, And Influence

Count's Kustoms Las Vegas Caddy Daddy Presents
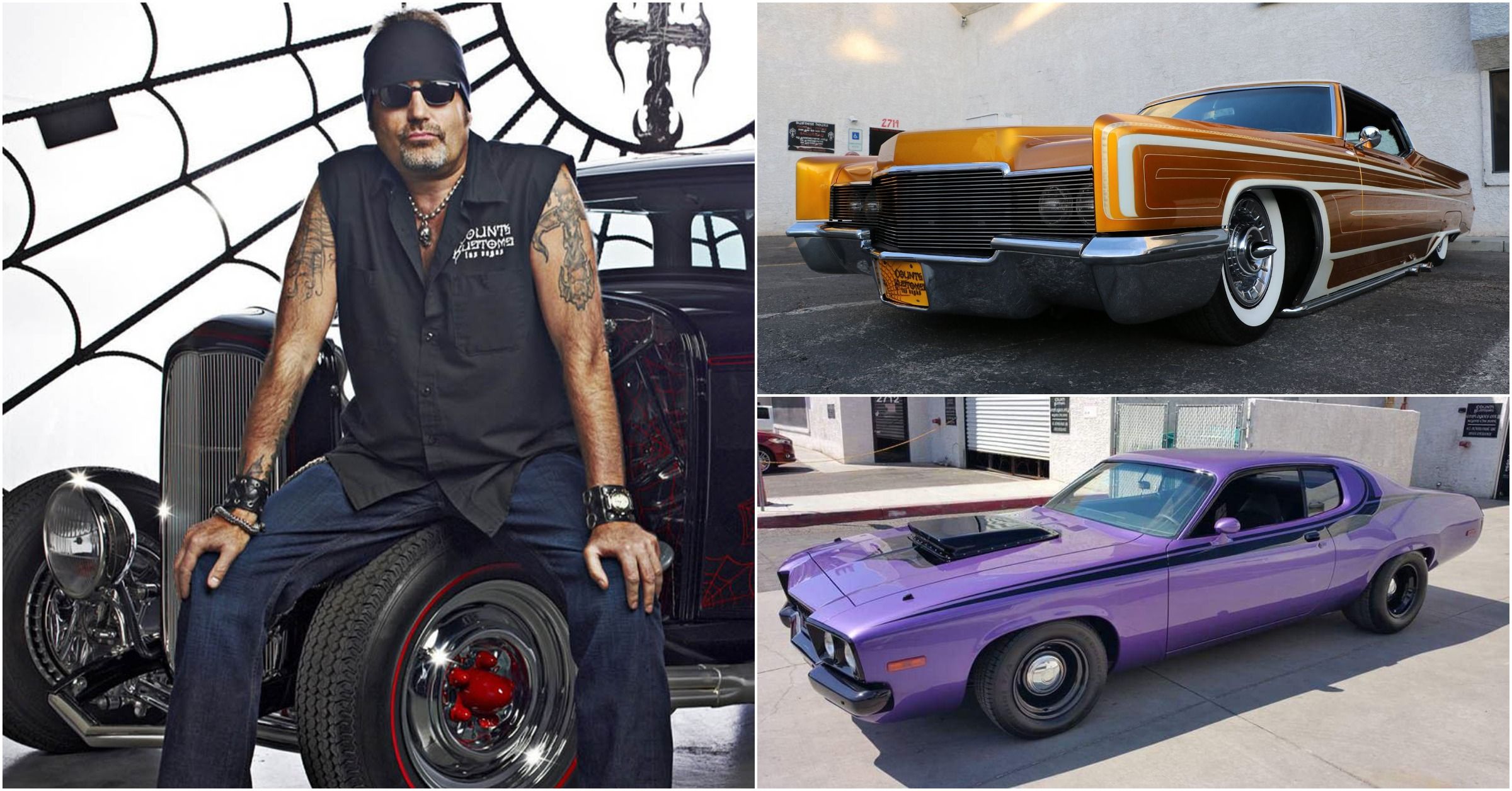
Count'S Kustoms Calendar Dalila Wanids